How Rotomolding Ensures Uniform Strength and Quality
Rotomolding, small for rotational molding, is a trusted manufacturing method that's acquired substantial acceptance for providing top quality, hollow plastic parts. This process involves heating plastic resin inside a spinning shape, allowing the product to equally coat the inner area and kind accurate, easy products. Their rising reputation stems from their ability to provide cost-effective, solid, and variable solutions across various industries. From industrial tanks to outside furniture, Rotomolding is a process built for both reliability and innovation.
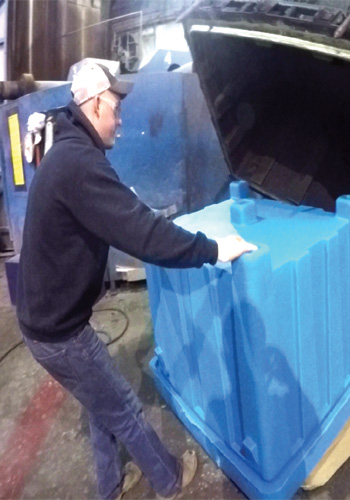
Extraordinary Toughness and Structural Strength
One of many standout advantages of rotomolding may be the toughness it brings to the ultimate product. The method ensures that plastic-type is consistently spread through the form, resulting in regular wall depth and strength. Unlike different molding methods, rotomolding minimizes poor spots, creating the finished products more tolerant to stress, affect, and environmental conditions. That helps it be suitable for outdoor or industrial programs where long-term performance is critical.
Cost-Effective Tooling and Generation
For firms seeking to produce low- to medium-volume services and products, rotomolding supplies a unique cost advantage. The tooling used in rotational molding is considerably less expensive than procedure or blow molding. That helps it be a functional choice for tailored areas or services and products that do not need bulk production. Decrease upfront expenses and successful substance use change into long-term savings, especially for little and medium-sized enterprises.
Design Flexibility and Modification
Rotomolding stands apart because of its power to allow for complex forms and custom designs. The procedure permits delicate facts, including inserts, threads, and numerous wall thicknesses—all within a single mold. This level of flexibility is beneficial for industries that want certain, tailored solutions. From agricultural gear to playground parts, rotomolding provides innovative flexibility without reducing on performance.
Smooth, One-Piece Construction
Another significant benefit of rotational molding is the manufacturing of smooth, one-piece items. That feature is very valuable for applications requesting watertight or airtight qualities, such as for example water tanks or fuel containers. Without stitches or bones that may damage over time, rotomolded items provide improved longevity and reliability. The absence of extra welding or construction also reduces work and product costs.
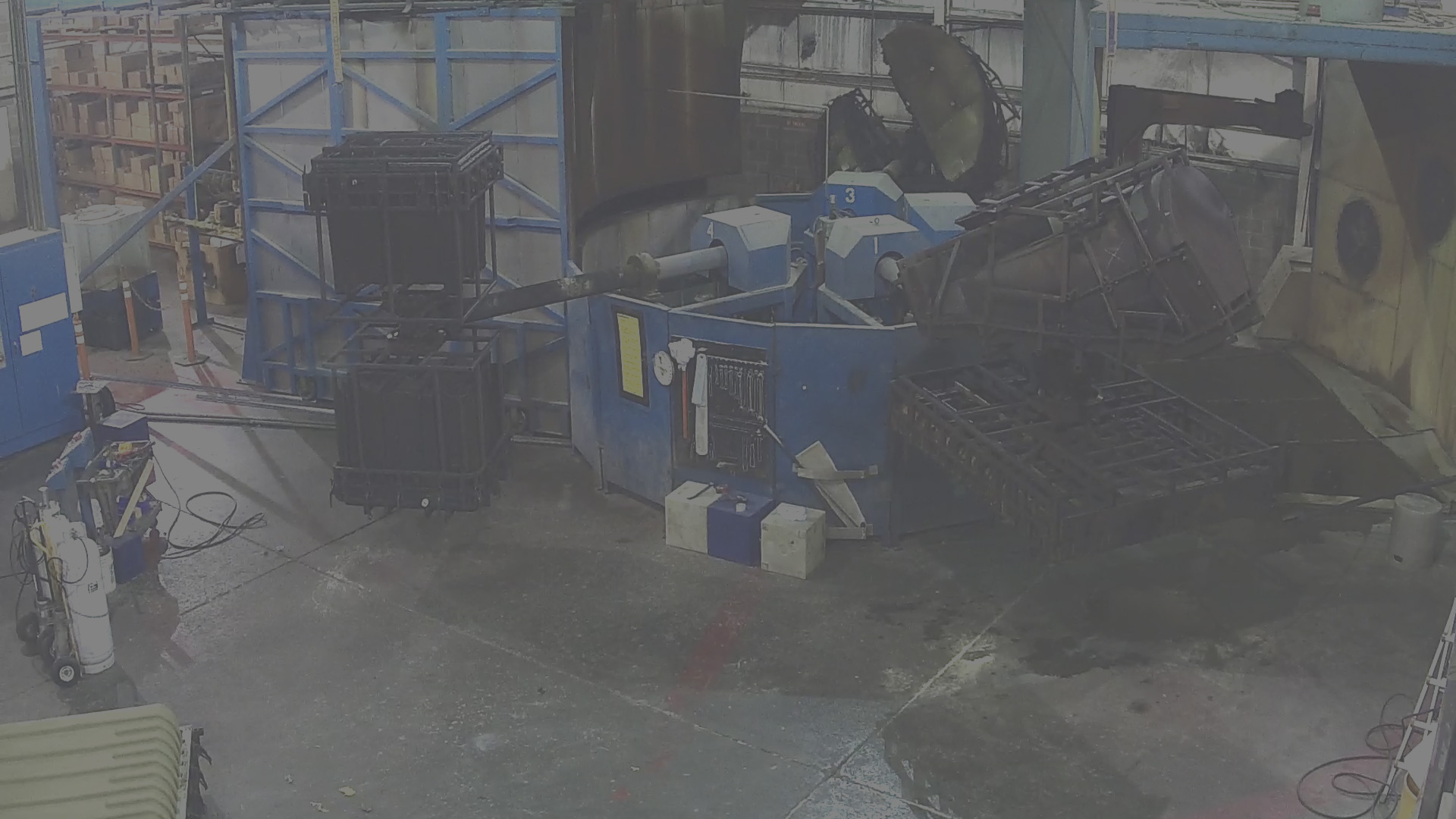
Eco-Friendly and Efficient
In the present environmentally conscious earth, the sustainability of manufacturing operations issues a lot more than ever. Rotomolding is known for their successful use of components and reduced waste output. The procedure is suitable for recyclable and UV-resistant pockets, encouraging equally environmental targets and item longevity. Also, their low-pressure strategy uses less energy in comparison to high-pressure alternatives.
Realization
Rotomolding provides a distinctive blend of durability, affordability, and style mobility that few different plastic manufacturing strategies may match. It suits a wide selection of industries with detail, cost-efficiency, and quality. Whether producing storage tanks, containers, or personalized plastic areas, the features of rotational molding allow it to be a smart, sustainable selection for contemporary manufacturing needs.